При возведении любого инженерно-технического сооружения особое внимание уделяется качеству сварных соединений, поскольку от них во многом зависит устойчивость конструкции к статическим и динамическим нагрузкам. К числу наиболее удобных методов проверки швов относится ультразвуковой контроль, позволяющий выявлять как поверхностные, так и скрытые дефекты в изделиях. На сегодняшний день такая дефектоскопия металлических соединений является обязательной процедурой, без которой сдача строительного объекта в эксплуатацию не допускается.
№ п/п | Наименование испытаний | Нормативный документ | Цена за ед. испытаний в руб. |
Сварные соединения | |||
1 | Контроль качества (дефектоскопия) сварных соединений (швов) ультразвуковым методом (1 п. м). | РД 34.17.302 СП 70.13330 |
4500 руб. |
Особенности проведения диагностики
Суть ультразвукового сварного контроля (УЗК) заключается в обработке сварного шва ультразвуком, в основе которого лежит анализ характеристик отраженной волны при помощи специального оборудования. Это один из простых, но эффективных методов контроля неразрушающего типа, позволяющего определить следующие дефекты:
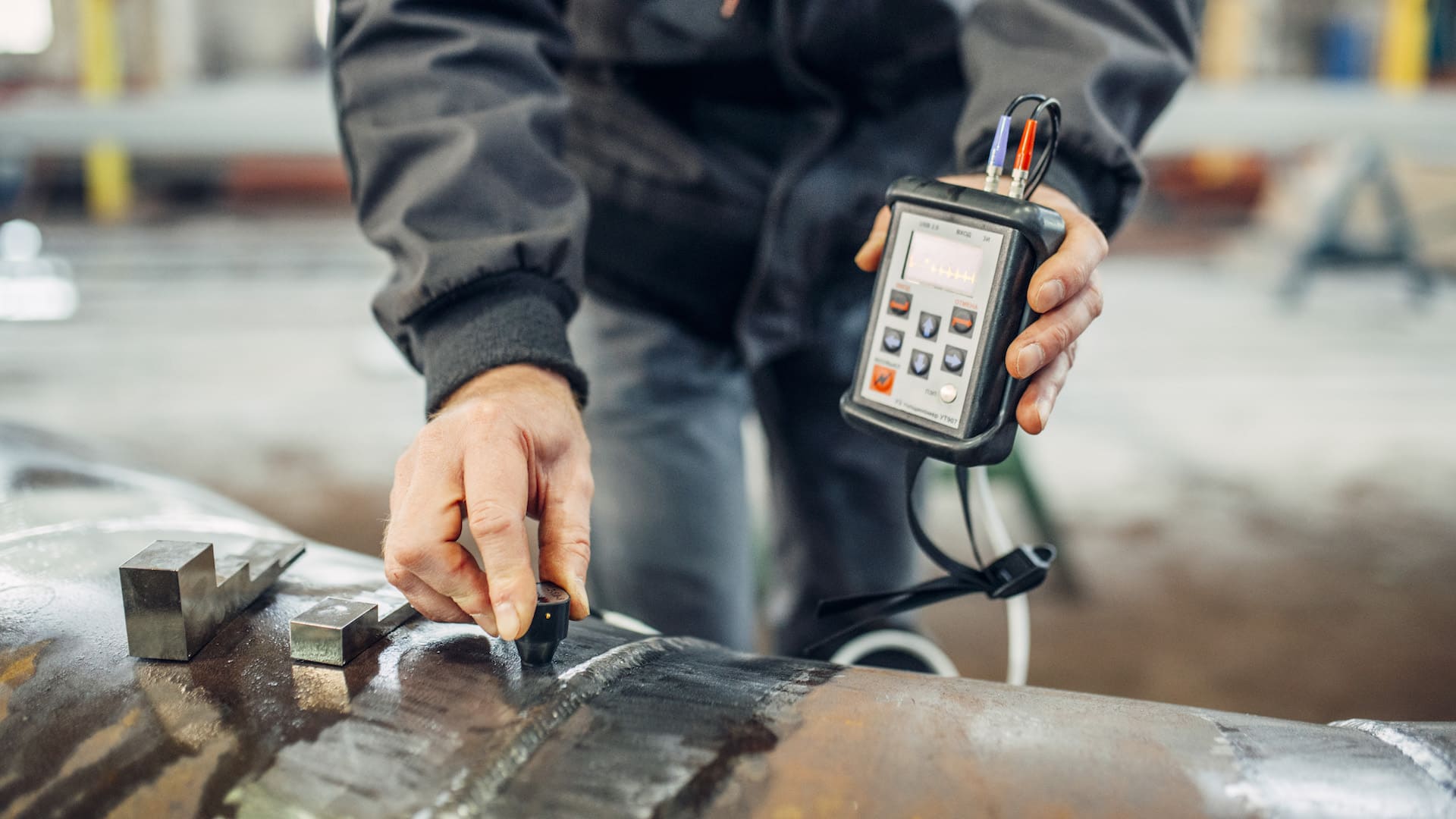
- недостаточный провар металла;
- коррозия и свищи;
- расслоение и поры;
- мелкие трещины в районе шва;
- выявление химического состава металла, несоответствующего регламентным требованиям.
Способ позволяет определить поверхностные и скрытые дефекты самых разных металлов, включая медь и латунные сплавы, чугун и аустенитная сталь (с крупнозернистой и мелкозернистой структурой). При помощи методики обнаруживаются даже мелкие изъяны в районе соединений, что позволяет специалистам сделать соответствующие выводы относительно его качества и надежности.
Применяемые методы проверки
Выделяют следующие способы проведения дефектоскопии, к числу которых можно отнести следующие:
- Зеркально-теневой метод. При таком способе дефект обнаруживается по коэффициенту затухания колебания, отражаемого от структуры металла.
- Теневой способ. В основе лежит контроль снижения уровня колебаний со стороны как прошедшего, так и отраженного импульса.
- Дельта метод. Здесь анализируются ультразвуковая энергия, которая отражается от потенциального дефекта.
- Эхо-зеркальный. Носит также название «Тандем», поскольку здесь используются два специальных аппарата, работающих синхронно и генерирующих колебания на единый приемник.
В основе вышеизложенных методов лежит анализ ультразвука, причем все они являются очень точными и достоверными, поэтому активно применяются при проведении лабораторных испытаний.
Этапы проведения ультразвукового контроля сварного шва

- Очистка поверхности стали с удалением лакокрасочного покрытия и пятен ржавчины на расстоянии 60-70 мм от места проверки с каждой стороны.
- Обработка металлической поверхности при помощи машинного масла, глицерина или иного состава с целью повышения точности процедуры за счет плавности скольжения.
- Настройка аппарата для процедуры дефектоскопии с учетом толщины и структуры конкретного металла (сплава).
- Непосредственное проведение работы, которое заключается в плавном передвижении щупа искателя особым зигзагообразным образом. При появлении на экране прибора устойчивого сигнала искатель разворачивают максимальным способом.
- Обнаруженные дефекты фиксируются прибором и заносятся в его память, после чего все данные анализируются экспертами.
Главным документом, определяющим стандарт проведения процедуры ультразвуковой дефектоскопии (УЗД) является ГОСТ Р 55724-2013, где прописаны методики исследования швов, выполненных разными способами сварки.
Достоинства и недостатки контроля УЗК
Для полного понимания всех особенностей такой экспертизы, стоит подробнее рассмотреть ее сильные и слабые стороны, что позволит понять, где и в каких случаях ее целесообразнее всего применять.
Преимущества метода:
- возможность использования для анализа на работающих объектах без необходимости в остановке производственного процесса;
- полная безопасность для специалистов, которые проводят анализ, так как звуковые волны не наносят вреда человеку в отличие от рентгеновских волн;
- отсутствие риска повреждения исследуемого объекта, поскольку сталь при анализе не подвергается разрушению;
- портативность УЗ-дефектоскопа, что делает прибор мобильным и удобным в транспортировке; возможность применения в «полевых» условиях;
- низкая стоимость услуги за счет простоты ее проведения специализированными организациями;
- высокая скорость выполнения процедуры, а также получение объективного и максимально точного результата.
Недостатки метода:
- невозможность получения точных размеров обнаруженных дефектов, поскольку по форме и размеру изъяны могут быть самыми разными;
- сложность анализа сварных соединений на металле малой толщины, что усложняет процедуру контроля на объектах, имеющих сложную криволинейную геометрию;
- потребность в очистке места шва от окалины, грязи, ржавчины, лакокрасочного покрытия и прочих компонентов, что влечет за собой дополнительные затраты времени;
- сложность анализа металла с высокой степенью зернистости, поскольку при такой структуре ультразвук сильно гасится, что снижает эффективность применения методики;
- отсутствие возможности выявления 100% потенциальных дефектов.
Наша компания «СтройЛаб-ЦЕНТР» занимается оказанием услуг в области комплексной проверки комплексов и сооружений на предмет выявления потенциальных нарушений. Большой штат специалистов состоит из экспертов, обладающих не только практическим опытом, но и углубленными знаниями, позволяющими производить ультразвуковой контроль соединений в соответствии с требованиями ГОСТа.
Высокий уровень материально-технического обеспечения позволяет нам активно применять самые точные дефектоскопы, при помощи которых мы получаем максимально объективную информации о качестве сварного шва. Лояльные цены позволяют обращаться к нам каждому клиенту, кто нуждается в такой проверке.
На основании выполняемой работы нашими специалистами составляется экспертное заключение, которое заказчик может предоставить в главный проверяющий орган – Ростехнадзор, дающий разрешение на принятие объекта в эксплуатацию. Ждем ваших заявок по телефону контактной связи +7 (495) 979-03-48!